Non Destructive Testing (NDT)
Home / Services / Non Destructive Testing (NDT)
NDT Services are provided as per following detail
Liquid Penetrant / Magnetic Particle Testing (Wet Fluorescent and Visible)
These tests are used for recognizing defects or imperfections in the in the Gas turbine rotary blades, Compressor Stationary Vanes, Turbine Stationary Nozzles, Turbine Shrouds, Liners, Combustion Transition Piece, Combustion Fuel Nozzles or Combustion Crossfire Tube and balance of plant (BOP) during outages at customer premises.
Remote Visual Inspections through Video Borescope
It is used for detection of internal cracks and corrosion of
- Turbines
- Generators
- Valves Internals
- Welding Internals of SS tubing
- HP & LP Combustion Chambers
- Heat Exchangers and Boilers tubes
Video borescope uses high-intensity light source and advanced image processing for clearer, sharper video and still image quality.
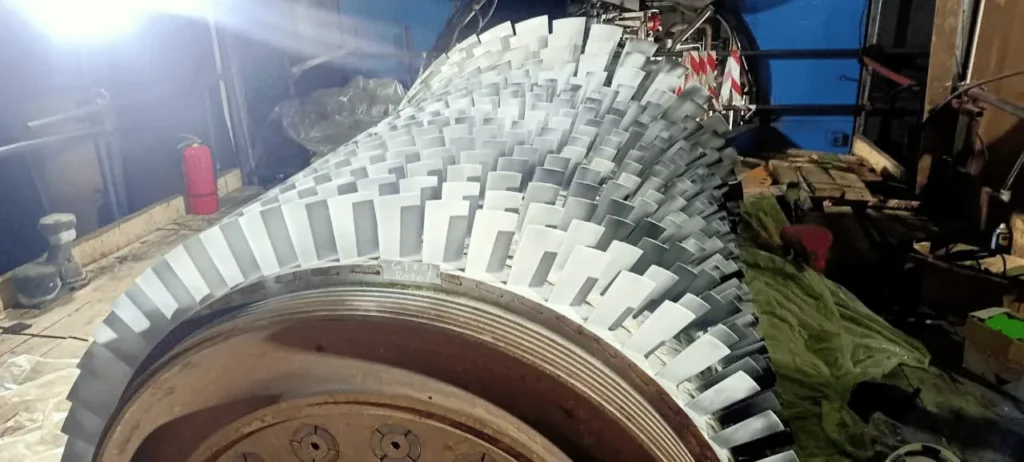
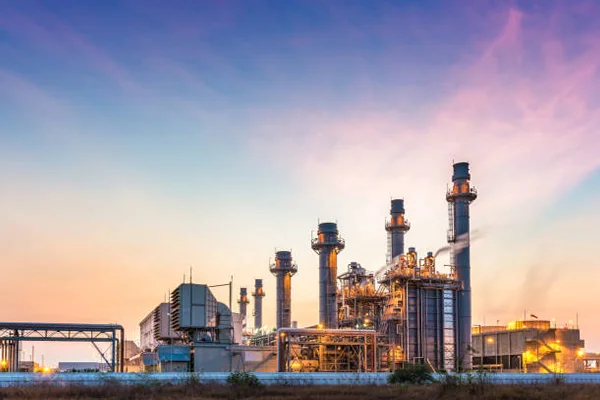
Ultrasonic Flaw Detection
Ultrasonic Flaw Detection is used to detect discontinuities in welds, adjacent heat affected zone, base metals made of steel or ferritic materials. This technique is also used for inspections of Shafts in Sugar Industry. It is used for dimensioning of indications for comparison with referencing code.
Typical types of discontinuities that can be detected by this method are cracks, incomplete fusion, incomplete penetration, misalignment, overlap, porosity, root-concavity, undercut, burn-through, excessive/ inadequate reinforcement, laminations, inclusions, etc.
Inspections is performed using Pulse Echo Technique by deploying probes B2S, MB2S, MWB 60-2, 70-2 for recognizing defects or imperfections in the shafts.
Interpretation of Tests
These tests are performed through qualified personnel, using approved consumables and calibrated Testing Equipment.
Interpretations of these test are performed as per customer specifications and relevant international standards